5S

A system for securing lubrication maintenance
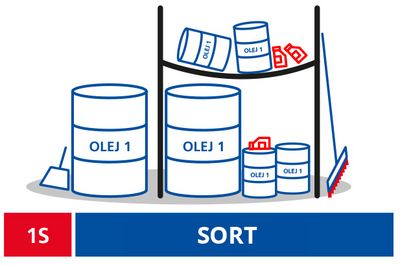
Sort by
- getting rid of products that are no longer used
- getting rid of products in the existing range that do roughly the same thing
- getting rid of lubrication equipment that is damaged or not up to scratch for some other reason.
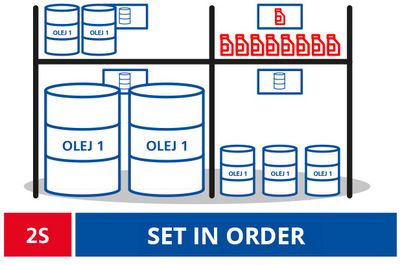
Sort in order by
- having a dedicated lubricant store
- labelling equipment and products so that everyone knows what’s what
- giving each type of grease its own sprayer and each oil its own can
- making sure that oil refill containers are sealed to keep dust and dirt out.
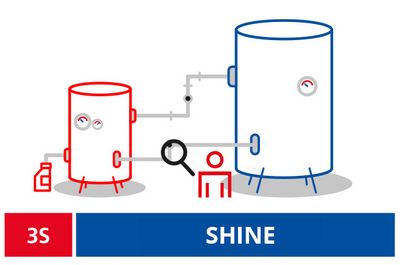
Shine by
- preventing spillage using absorption materials and oil collectors
- cleaning around lubrication points and in the oil store
- cleaning and tidying a little every day, and doing a main clean once a week
- setting a standard and making sure it’s on the checklist.
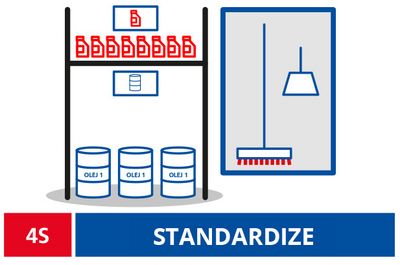
Standardize by
- making a to-do list for support and continuity, e.g. in oil changes, analyses, machine care and cleaning
- having control procedures to assure work on labelling, cleaning and good order
- including the measures in lists/standards in maintenance systems or in Excel so they are easy to find, follow and update.
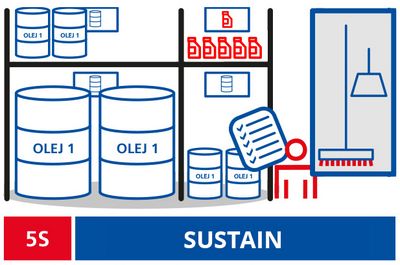
Sustain by
- drawing up checklists for all 5S work, ensuring that good order is maintained and can be gradually improved
- carrying out regular audits/inspection patrols, and recording them with text and images
- making sure that the follow-up results are concrete and discussed with everyone who works with lubrication maintenance
- making sure that the follow-up results are concrete and discussed with everyone who works with lubrication maintenance
- highlighting the benefits, and the fact that systematic maintenance leads to a cleaner, safer, more efficient workplace.