Filling lines offering reliability and flexibility
Our filling lines are the processes we use to fill our various product packs. In conjunction with the relocation to Fors we are now testing all the equipment for the various filling lines, both new and existing. Karin Lagerstedt is the Senior Manager Engineering, responsible for the tests.
We have filling lines for packs from 1L up to drums and IBCs. Two of the six filling lines we’re now starting up in Fors are flexible and can be used for several pack sizes. For the new plant, we’re investing in new lines and moving some of the existing ones which we feel work well, from the current plant in Nynäshamn. Both the new and old equipment will be tested on site in Fors and optimised for stable, efficient filling.
Testing all the equipment for the filling lines involves a lot of work: each pack has to be filled and weighed, sealed and labelled, and then wrapped and packed onto pallets for transport to the customer. Each individual part of the equipment is critical, which is why it’s also important to carefully test all the various parts of the filling lines.
"All these tests also serve to heighten the expertise of our operators. In the longer run, this also means added peace of mind for our customers."
One of the major benefits of the new equipment is the capability for automatic switching between different pack sizes. We also now have great flexibility and high reliability with parallel systems. To ensure successful start-up of the new equipment, we first conducted comprehensive Factory Acceptance Tests, or FAT, at suppliers’ sites using our own packing materials. We are now also conducting our own tests on site at the new plant, to ensure correct installation and so minimise the risk of problems later on.
All these tests also serve to heighten the expertise of our operators. While we do already have excellent knowledge about the complexity in our older equipment, these tests will make our operators experts on how the existing and the new, modern equipment work, down to the finest detail. In the longer run, this also means added peace of mind for our customers. The objective is to lay the best possible foundation, so that our customers get the same great products they’re accustomed to, also moving forward.
One unexpected challenge is of course the coronavirus pandemic. There are a lot of people involved in a project of this scale, and a lot of it is about coordinating different suppliers.
We always select our suppliers carefully and have suppliers in different parts of Europe. Despite the pandemic, it looks like we’re well on target to meet our schedule. We are testing the filling lines in June and July.
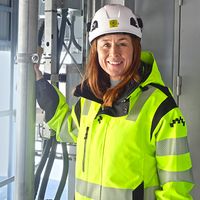