5 Questions with Ed Banashak: Cement Lubrication
With more than 40 years of experience in the lubrication industry, Ed Banashak works with customers in the cement industry to optimize lubrication strategies, boost machine efficiency, and maximize uptime. We sat down with Ed to ask him about the latest trends in the cement industry, how lubricants can play a role in addressing these challenges, and tips for getting the most out of your lubrication plan.
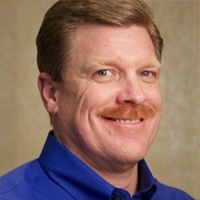
1. What are the primary challenges in selecting the right lubricants for cement plant equipment?
Cement plants operate under harsh conditions that include extreme temperatures, high loading on equipment, and the presence of significant contaminants, all of which must be considered when selecting the right optimum lubricants for cement plant equipment. It is important to select lubricants that provide good contamination control as dust and debris can reduce a lubricant’s effectiveness. Rotary kilns, crushers and conveyors each have different lubrication needs, making it difficult to select a single solution that will meet all their requirements. Selecting the right lubricants that provide protection for all temperature, load, and speed variations in your application is essential. Lastly, it is important for a plant to implement a well-organized maintenance plan to ensure lubricants are applied properly, at appropriate intervals, and monitored for integrity in a proactive manner.
2. In your experience, what is the most overlooked aspect of lubrication that could drastically improve operations in the cement industry?
One of the most overlooked aspects of lubrication that could drastically improve operations in the cement industry is greasing frequency on components like bearings and open gears. Proper lubrication at the right intervals is essential for optimizing equipment performance and efficiency. In many cement plants, grease is often not applied correctly or frequently enough, which can lead to increased wear, high temperatures, and equipment failures. Regularly scheduled lubrication that is appropriate for the specific needs of each piece of equipment can significantly reduce downtime, improve energy efficiency, and extend the lifespan of machinery. FUCHS can support this objective with programs implemented and supported by our experts.
3. What should be considered when selecting lubricants for environments with high dust contamination, such as those found in cement plants?
Selecting lubricants with the correct viscosity for your operating conditions ensures the lubricant can provide a protective film over the equipment surfaces. Lubricants with high-temperature stability are critical to prevent the lubricant from breaking down and anti-wear and EP additive packages can help protect equipment from abrasive wear, even in the presence of significant contaminants like dust. Application methods like automatic lube systems can ensure consistent and precise application to reduce the risk of contamination during manual lubrication. Implementing a regular monitoring and maintenance schedule can help you identify contamination and assess lubricant performance. FUCHS' Smart Service Program and expert representatives offer the support and information needed to choose the best solution for your application and environment.
4. How does lubrication affect energy efficiency in cement plants, and what steps can be taken to reduce energy consumption through better lubrication practices?
Cement customers are looking for innovative lubrication solutions for grinding, kilns, trucks, and other equipment that can provide energy reduction and reduce the CO2 footprint for the company. FUCHS has developed the most modern lubricant formulations that offer lower friction to address this demand. Proper lubrication reduces friction between moving parts, which helps reduce energy. Wear reduction also helps extend the lifespan of components such as motors, gearboxes, and bearings, thus reducing waste. Lubrication helps protect equipment from contaminants such as dust and moisture, thus enabling the machine to operate more efficiently and draw less energy.
5. What trends do you see in the future of lubrication for the cement industry, particularly regarding automation and smart technologies?
The cement industry is increasingly focused on implementing new technologies aimed at improving sustainability and minimizing environmental impact. This shift emphasizes the need for suppliers and partners who can provide comprehensive programs, including lubricants, materials, services and technical training, to support these objectives. FUCHS offers advanced products engineered to withstand extreme environments while reducing lubricant and energy consumption. For example, CEPLATTYN GT reduces open gear consumption by up to 30% and lowers wear rates. Additionally, our gear oils last 3 to 5 times longer than standard gear oils, cutting customer consumption by up to 80%. We can also extend re-greasing intervals with our advanced polyurea, and calcium sulphonate greases. All these benefits are backed by FUCHS’ highly skilled field representatives.