Lubricants for Semiconductor Manufacturing
MOVING YOUR WORLD by striving for perfection and unconditional reliability
FUCHS is the leading provider of specialty lubrication solutions for semiconductor manufacturing equipment and cleanroom applications. With hundreds of sequential steps involved in semiconductor fabrication, contamination of any kind can result in costly downtime. Low-outgassing vacuum lubricants from our NYETORR and NYECLEAN product lines help prevent contamination and improve the performance and reliability of components in fabrication and processing equipment to improve line yields, avoid latent defects, and increase uptime.
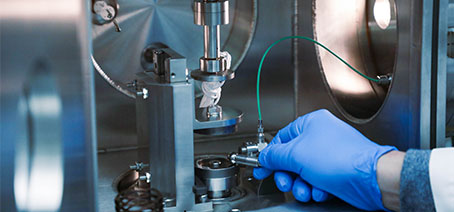
Technologically Leading
We don't just develop lubricants, we develop intelligent solutions for highly complex challenges. Our lubricants are tested in our state-of-the-art laboratory where their performance can be validated under vacuum, extreme temperatures, and conditions relevant to your application. Our experts have an in-depth understanding of your application and are ready to work with you and assist in selecting the correct lubrication solution for your operations.
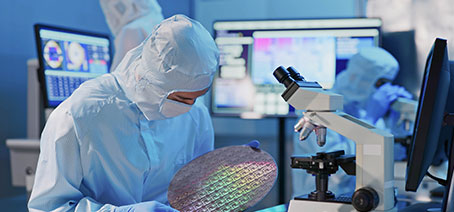
Proven Solutions
As a trusted lubrication partner to the industry’s top semiconductor manufacturing OEMs, we create tailor-made solutions that draw on over 90 years of experience. For these specialized applications we formulate lubricants using the highest-quality raw materials available today. Allowing you to benefit from an unbeatable combination of both proven practice and individual solutions. Our data-backed solutions help us fulfill our promise to you: unyielding reliability.
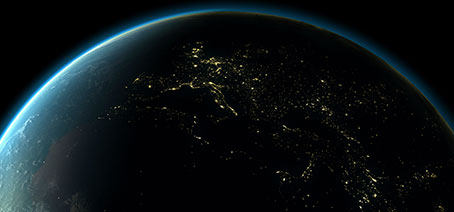
Globally Present
Our customers have access to our global distribution network with the convenience of local support. Our products for the semiconductor industry adhere to uniform standards to ensure customers around the world experience the same excellent performance. FUCHS holds itself to the highest quality standards. Our in-vacuum lubricants are manufactured and packaged in our ISO Class 8 and Class 7 certified clean rooms to reduce risk for our customers.
Lubricant Advantages
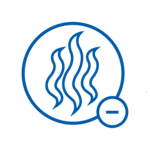
Outgassing is akin to evaporation; it is the release of small fractional molecules from a bulk liquid or solid material. Evaporation losses accelerate when operating in vacuum and compromise a lubricant’s integrity over time. Low outgassing lubricants have a lower material loss to ensure longer-lasting lubrication. Outgassed molecules can also condense on surfaces and contaminate wafers, processing equipment, and other sensitive components. Lubricant outgassing is measured in total mass loss (TML) and collected volatile condensable materials (CVCM) per ASTM E595. Our lubricants are tested to this standard to meet the stringent outgassing limits determined by the semiconductor industry.
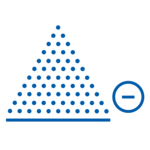
Dynamic particle generation happens when contaminants are created by being forced or expelled from a lubricated ball-screw, bearing, or gear system into the operating environment. These contaminants could include base oil constituents, thickener particles, additives, etc. and are freed from the grease through rolling, sliding, or a combination of both. Our proprietary test method and apparatus allows us to measure particle generation under these dynamic conditions.
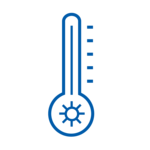
A lubricant must be able to protect the mechanical components of fab equipment at high temperatures without evaporating. Outgassing is more likely to happen at high temperatures as vapor pressure increases. Many of our in-vacuum and cleanroom lubricants are formulated to perform at temperatures up to 250 °C.
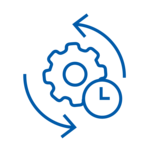
Our semiconductor lubricants offer long service life even under harsh in-vacuum conditions to extend maintenance intervals. Originally developed by NASA to evaluate space applications, the Spiral Orbit Tribometer is an ultra-high vacuum test whose results indicate the relative life expectancy of a lubricant.
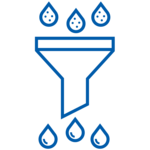
Manufacturing equipment in vacuum and cleanroom environments are highly sensitive, where even microscopic particulates can cause friction and positioning errors. The best way to ensure lubricant cleanliness is through ultrafiltration to reduce microscopic particulates in a lubricant. We can ultrafilter grease and oil to reduce possible contaminants for semiconductor applications.
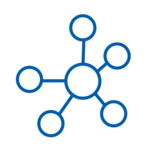
All of our products for semiconductor manufacturing equipment use PTFE with levels of PFOA less than 25 ppb weight, in compliance with current REACH and other international regulations. Although this work is not a measurement of each product’s complete formulation, analysis indicates PTFE would be the most significant contributor to PFOA-levels. The regulatory environment around perfluorinated-alkyl substances (PFAS) remains uncertain, but our R&D team is conducting leading research into the development of non-PFAS-based solutions for the semiconductor industry, ensuring that we will be prepared in the event of more stringent regulations.
Lubricants for Semiconductor Robotic Systems
PFPE and MAC-based lubricants are recommended for vacuum environments because of their low vapor pressure, and low outgassing. PFPE lubricants offer better high temperature performance (up to 250° C) when compared to MAC lubricants (up to 150° C). Because of their unique additive packages, MAC lubricants provide better protection against wear when compared to PFPE lubricants. Both chemistries can be ultrafiltered, are compatible with plastics and elastomers, and comply with PFOA regulations.
To meet such stringent precision requirements, lubricants for bearings and gears in semiconductor manufacturing equipment must prevent wear, offer long-life lubrication and minimize friction torque. These lubricants must meet cleanliness requirements, resist corrosion in environments that contain aggressive process gasses or chemicals, and maintain their consistency in service with minimum dynamic particle generation. Lubricants must be formulated to ensure the appropriate film thickness to reduce friction between moving parts and prevent wear and component seizure. Under vacuum process conditions, gears and bearings can be exposed to ultra-high vacuum, high temperatures, harsh chemicals, and corrosive and oxidative gases. This environment requires lubricants with low outgassing and low dynamic particle generation, chemical inertness, long life, and excellent wear resistance.
PFPE lubricants: NYECLEAN 5057 & 5097R and NYETORR 5300, 5300XP, 6300 & 6300S
MAC lubricants: NYETORR 5200, 6200 and 6200-FL
Semiconductor automation, robotic and wafer positioning systems use linear guides, slides and ball screws/lead screws to enable highly precise movements. Lubricants are essential to help reduce friction and wear in a linear guide system and to maintain running accuracy and repeatability. Lubricants must also exhibit excellent vacuum stability, chemical resistance within vacuum processing and cleanroom environments, and outstanding “stick-slip” performance.
PFPE lubricants: NYETORR 5300XP, 5350
MAC lubricants: NYETORR 5200, 6200, and 6200-FL
High-performance valves control the flow rate and pressure of fluids and must offer reliable, fast, and accurate control which requires the use of high-performance lubricants. Greases for lubricating valves are similar to those used for lubricating gears and bearings, with the additional requirement to remain in place under high differential pressures which may require a stiffer consistency formulation.
PFPE lubricants: NYETORR 5300 & 6300
MAC lubricants: NYETORR 5200 & 6200
O-rings and seals play an important role in maintaining ultra-high vacuum in process tools and containing chemistries and gases within varying environments. O-rings and seal failure can cause a loss of vacuum and result in significant safety concerns and costly impacts to the manufacturing process. Properly selected lubricants can improve the performance of these components and extend their service life by minimizing friction and wear. The lubricants must exhibit low outgassing and low particle generation, chemical inertness, resistance to solvents, high thermal stability, low friction, low oil separation, and good stability. Lubricants must also be compatible with synthetic elastomeric polymers such as fluoropolymer elastomers, which are most often used to make O-rings and seals.
PFPE lubricants: NYETORR 5300, 6300 and 5381