ECOCOOL GLOBAL 20
The culmination of years of intensive research and development and recipient of multiple patents, FUCHS ECOCOOL GLOBAL 20 represents a milestone in metalworking fluid design. The solution allows automotive OEMs and suppliers for the first time to use a single metal cutting fluid for the manufacture of components from engine blocks, pistons and brake systems to wheels, gears and driveline components.
FUCHS ECOCOOL GLOBAL 20 has been designed to meet the varied requirements of different OEM and supplier stakeholders, including leaders responsible for the safe, efficient running of production facilities and equipment.
Development Highlights
Free of current and future restricted chemicals including boron, secondary amines, formaldehyde release biocides, chlorine, and TEA
Meets the national chemical inventory requirements of the top industrialized countries
Effective on multiple metals and across a wide range of water sources
Certified non-irritating properties enhance workplace environment
Near odorless characteristics increase operator acceptance
Available globally
Watch Global 20 In Action
LOW RESIDUE
ECOCOOL GLOBAL 20 is mixed with water and baked in an oven for 24 hours. Dried residue washes away completely in less than 60 seconds with gentle rinsing.
RESISTANCE TO FOAM
Tired of foam? It certainly is a poor lubricant and doesn't transfer heat very well! ECOCOOL GLOBAL 20 foams up to 56% less than three leading industry coolants.
HIGH EASE OF MIXING
Mixes easily when making manual tank-side additions.
HIGH LUBRICITY
Formulated for use on multiple metals and designed to increase your productivity, tool life and enhance part finish.
End to end solutions
- Increases machine uptime
- Higher production rates
- Fewer work stoppages
- Reduces system cleanouts
- Longer tank life
- Lower consumption
- Reduces coolant purchase cost
- Reduces waste disposal cost
- Eliminates (or reduces) tank-side additives
- Reduces environmental impact
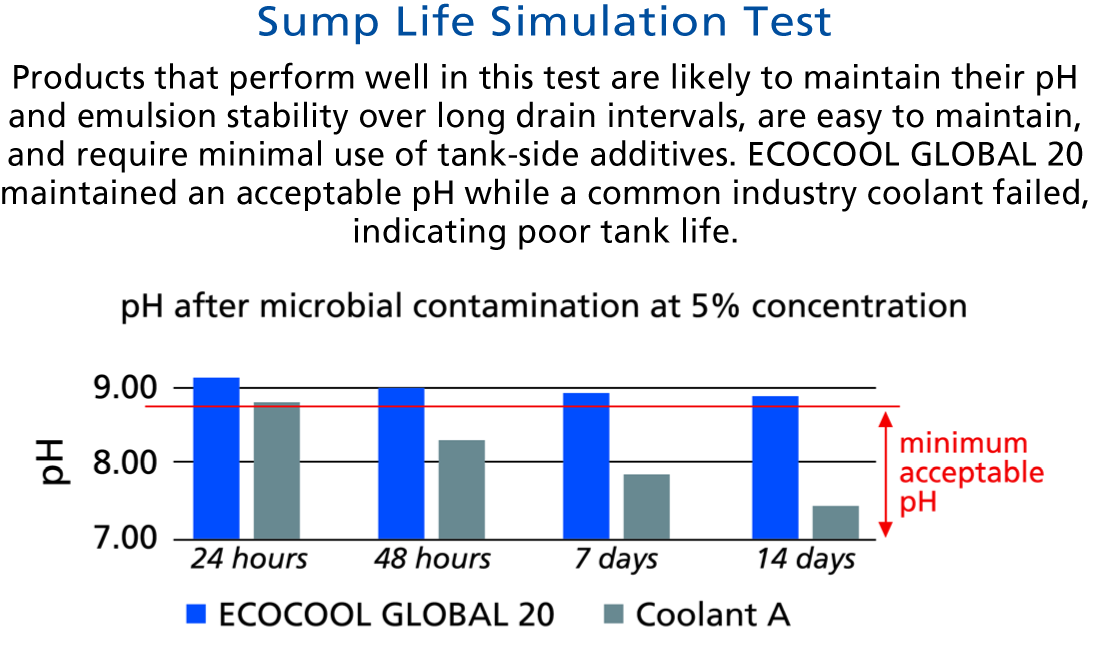
- Increases production
- Accelerates cutting
- Increases feed rates
- Improves surface quality
- Lowers rework costs
- Reduces scrap costs
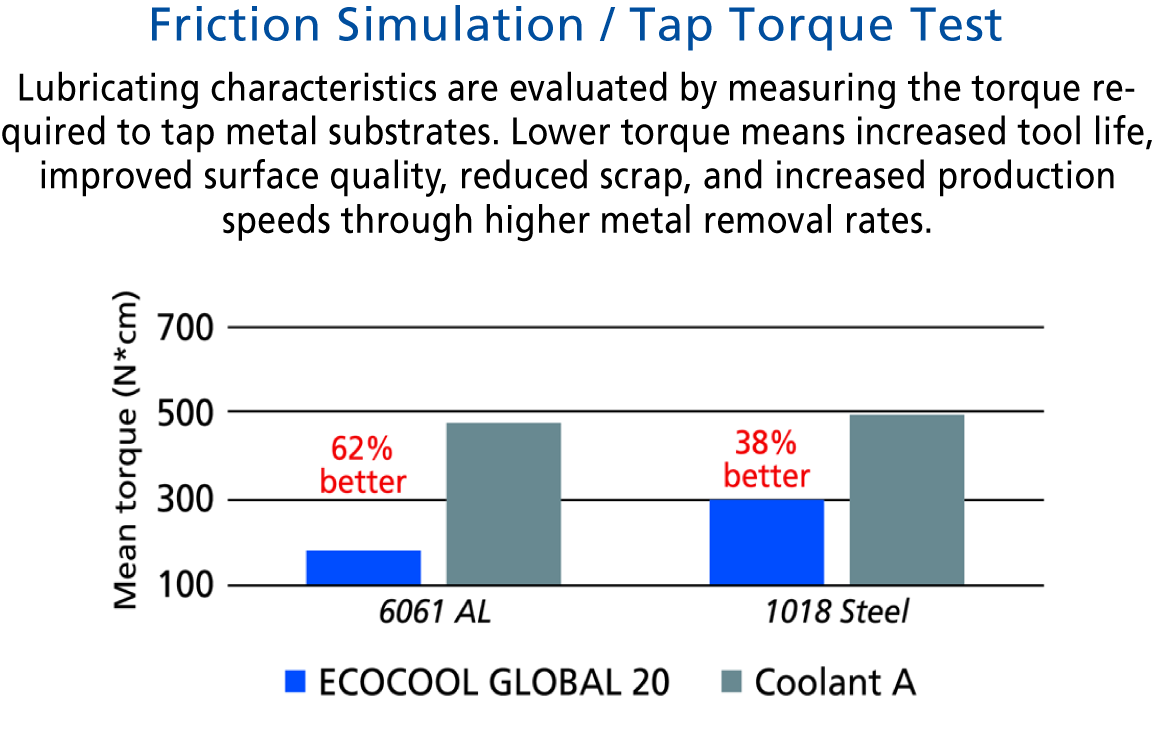
- Increases operational flexibility
- Expands use across multiple departments
- Eliminates the need for multiple coolants
- Reduces operational complexity
- Reduces inventory complexity
- Reduces costs
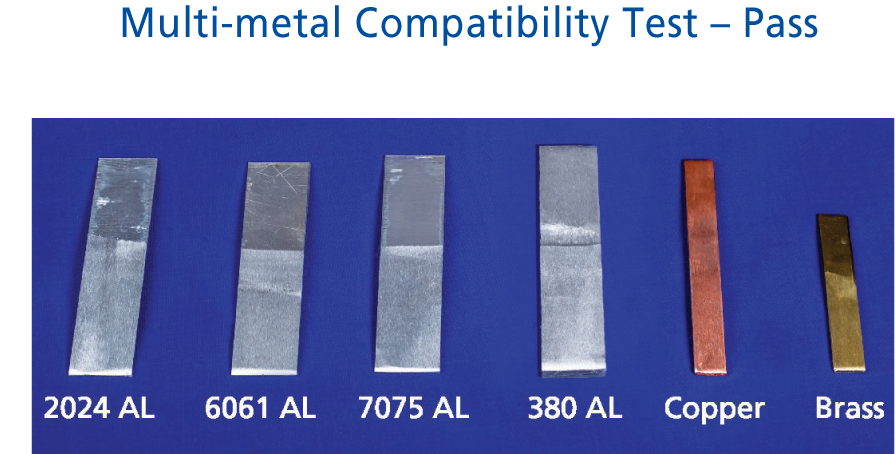
- Reduces maintenance time
- Minimizes work stoppages
- Improves tool life
- Improves surface finish
- Reduces rework costs
- Reduces tool costs
- Reduces consumption
- Reduced housekeeping
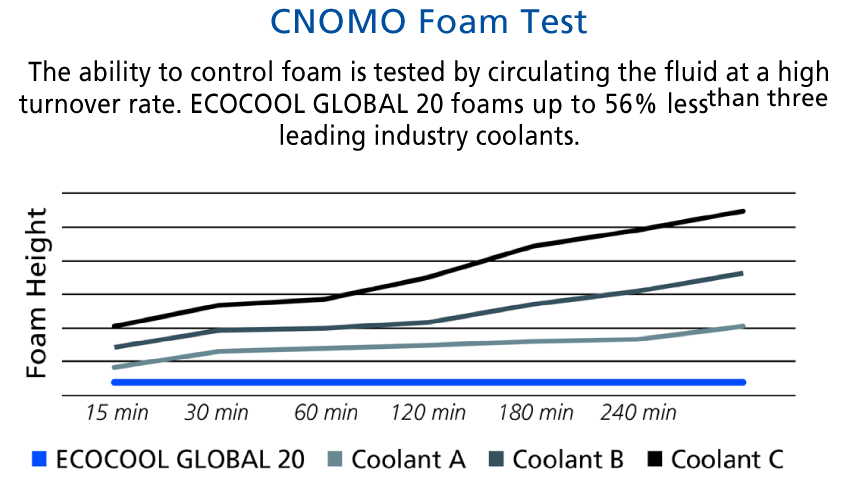
- Eliminates emulsion splitting
- Extends coolant lifecycle
- Eliminates residues
- Reduces consumption
- Reduces maintenance time
- Eliminates (or reduces) tank-side additives
- Reduces costs
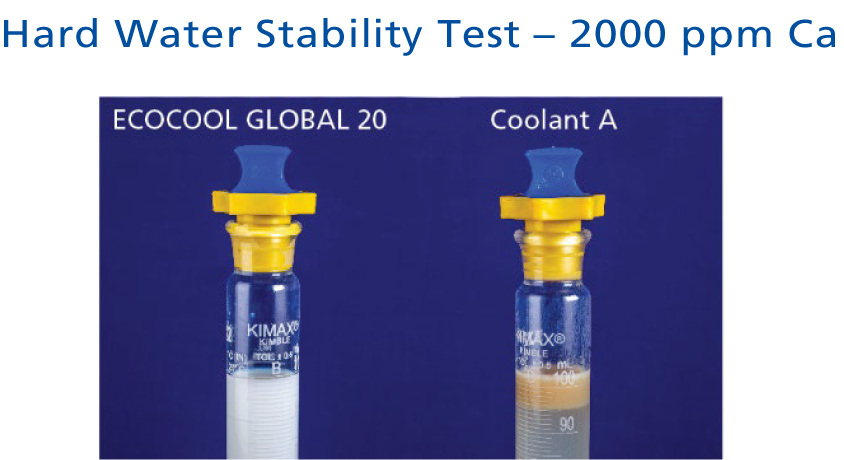
- Proven non-irritating to skin
- Nearly odorless
- Enhanced workplace environment
Skin Irritation Test
The Bovine Udder Skin (BUS) test is an industry acceptable method of predicting a chemical’s effects on human skin. ECOCOOL GLOBAL 20 is designated as “not irritating” to humans by a certified third-party lab.
- Complies with most corporate restricted chemicals lists and the National Chemical Registry simplifies implementation
- Approval from the 19 top industrialized countries enables global roll-out and use
- Available globally
- Global support network provides peerless technical services
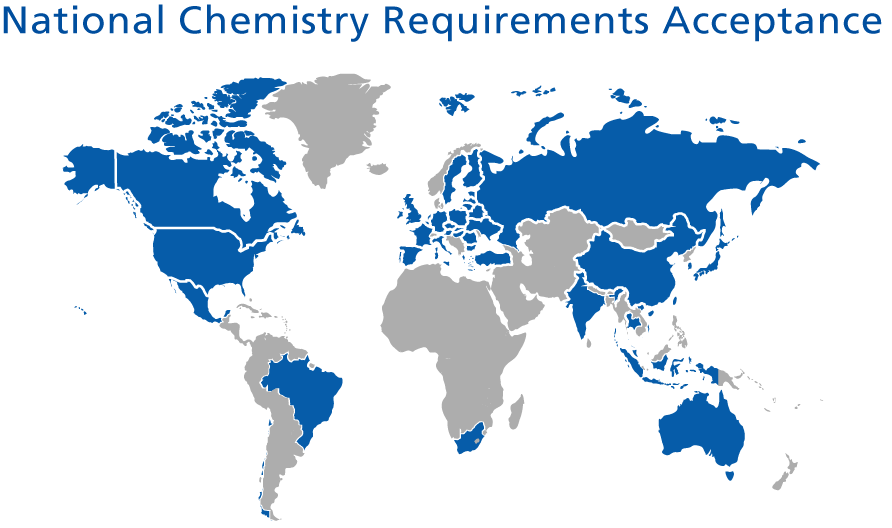
Proven Performance
Operational Specifications
Machine Tool: Cargill Detroit Dial Machine
Materials | Operations | Tooling | Sump Size |
|
|
|
|
Customer-Reported Improvements
- Tool life improvement X3
- Eliminated foam
- Reduced residue
- Lowered costs
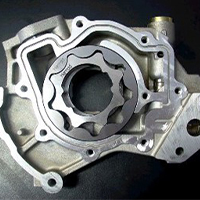
Operational Specifications
Machine Tool: Oberlin Grinders
Materials
| Operations
| Tooling
| Sump Size
|
Customer-Reported Improvements
- Eliminated foam
- Eliminated rust
- Eliminated bacteria
- Eliminated machine residue
- Lowered costs
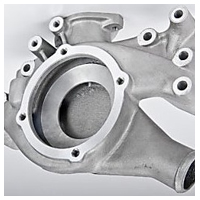
Operational Specifications
Machine Tool: Gildemeister GMX 250
Materials
| Operations
| Tooling
| Sump Size
|
Customer-Reported Improvements
- Lowered cost
- Less consumption (drag out)
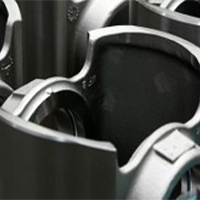
Operational Specifications
Machine Tool: Makino, Mazak
Materials
| Operations
| Tooling
| Sump Size
|
Customer-Reported Improvements
- Longer tool life
- Eliminated foam
- Longer tank life due to stable emulsion
- Lowered costs
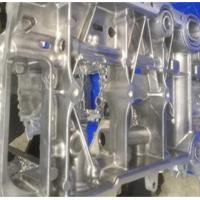